Qu'est-ce que la méthode Kaizen ?
Née dans l’industrie manufacturière du Japon, la méthode kaizen s'inscrit au cœur du lean manufacturing et du lean six sigma chers à Toyota. Le but de cette approche est d'optimiser la productivité grâce à l'amélioration continue des processus, des activités, l'élimination des gaspillages, la diminution des risques, l'optimisation des postes de travail. Elle repose sur 10 principes clés.
Quelle est sa philosophie ?
Contrairement à la recherche d'innovations de rupture et au reengineering, la philosophie du kaizen repose sur l'idée que de petits changements rapides et réguliers peuvent avoir des impacts forts. Simple dans le principe, la mise en oeuvre se révèle parfois compliquée.
A savoir : bien qu'utilisés dans l'industrie, les principes du Kaizen peuvent être mis en oeuvre dans d'autres secteurs d'activités comme les services, le commerce ou bien encore pour votre propre efficacité personnelle.
Quels sont les principes du Kaizen ?
Il s'agit du point le plus important de ce dossier. Il est commun d'évoquer 10 principes, même si, selon les sources, le contenu de la liste diffère. Ce sont les déterminants de l'esprit kaizen. Nous l'avons vu, ce n'est pas un outil, mais plutôt un état d'esprit reposant globalement sur plusieurs principes, une culture de l'amélioration continue, prônant :
- Chercher à s’améliorer en continu
... même quand tout fonctionne. Une démarche par petits pas mais régulière, qui vise le progrès durable. Etre proactif dans la résolution des problèmes : ne pas attendre leur apparition, anticiper et agir sont les maîtres mots. Utiliser les outils de la qualité comme les cercles qualité. Il est important de piloter son organisation à l'aide d'indicateurs de performance pour en mesurer les résultats.
- Impliquer tous les collaborateurs
L’amélioration est l’affaire de tous. Chaque salarié peut contribuer, à tous les niveaux.
- Remettre en question des standards
Ne pas s’en tenir à “on a toujours fait comme ça”. Tout peut être revu, testé, optimisé. Ne jamais considérer qu’un processus est optimal. Remettre régulièrement en cause les pratiques en place pour identifier des pistes de progrès. Refuser le statu quo. ne pas se satisfaire des solutions qui fonctionnent, chercher à s'améliorer en permanence, évaluer et optimiser les méthodes et les procédures de travail. Utiliser le benchmarking pour identifier les meilleures pratiques. Cela concerne les "gros" travaux mais aussi des petites améliorations. Dans la philosophie japonaise, des petits pas permettent d'avancer.
- S’appuyer sur des faits, pas des suppositions
Observer sur le terrain, analyser concrètement. Utiliser la méthode des 5 pourquoi pour aller à la racine des problèmes. Rechercher la cause première d'un problème avec la méthode des 5 pourquoi : ne pas se cantonner aux apparences, creuser dans la compréhension du "pourquoi racine" pour agir là où il faut.
- Éliminer les gaspillages
Supprimer tout ce qui ne crée pas de valeur : tâches inutiles, attente, défauts, mouvements inutiles (voir plus bas les 3 muda - sources de gaspillage)
- Rechercher des solutions simples
Préférer des idées concrètes et faciles à mettre en œuvre, plutôt que des projets complexes ou coûteux.
- Respecter les personnes et le collectif
Créer un climat de confiance. Écouter, encourager, valoriser les initiatives du terrain. Reconnaître les avancées, même modestes. Cela entretient la motivation et ancre une dynamique positive dans les équipes. N’oubliez pas : une idée simple, même sans budget, peut déclencher un vrai changement. Favoriser l'empowerment pour que les salariés deviennent acteurs dans la résolution des problèmes. Favoriser les prises de décision collaboratives : il vaut mieux demander l'avis de plusieurs personnes pour confronter les points de vues et enrichir l'analyse par des angles différents plutôt que décider seul dans son coin. Valoriser les petites victoires et les idées simples.
Autre point : travailler sur les processus, pas blâmer les individus. Les erreurs sont souvent le résultat de dysfonctionnements dans l’organisation. Corriger le système plutôt que de chercher des coupables.
- Standardiser les bonnes pratiques
Une amélioration efficace doit être formalisée pour devenir la nouvelle base de travail.
- Corriger les erreurs dès qu’elles apparaissent
dysfonctionnements ou erreurs, Ne pas laisser les choses s'installer, il faut passer à l’action, même de façon imparfaite. Mieux vaut mettre en place une solution partielle tout de suite que d’attendre la solution idéale. L’amélioration continue repose sur des progrès concrets, même imparfaits. Construire des plans d'actions, mener des actions correctives.
- Rechercher des solutions au moindre coût :
Dans la philosophie Kaizen, la révolution passe par des petits ajustements indolores financièrement. Il n'est pas question de tout jeter et recommencer. Le mot "investissement" ne fait pas parti du langage utilisé.
A noter : les systèmes de management de la qualité s'inscrivent dans cet esprit. Voir la norme ISO 9001 version 2015. La dynamique d'amélioration continue est souvent assurée par le responsable qualité.
Les 3M - Les 3 types de gaspillage
La réduction des gaspillages est un fil conducteur dans une méthode d'amélioration continue. Elle se matérialise par la méthode des 3M, identifiant les 3 sources de gaspillage :
- Muda : activité qui n'apporte pas de valeur ajoutée (stock dormant, surproduction, déplacement inutile d'un opérateur, etc.). Il est fréquent d'entendre parler des 7 mudas :
- Mouvement inutile : déplacement de personnes qui ne sert à rien. Exemple : organiser une réunion nécessitant la présence physique des participants alors qu'une réunion virtuelle aurait été suffisante.
- Temps d'attente inutiles
- Transports inutiles : déplacement sans valeur ajoutée
- Traitements inutiles
- Surproduction : produire plus que nécessaire
- Surstockage : stock surdimensionné
- Non qualité : défaut des pièces ou de qualité de service nécessitant généralement une tâche additionnelle.
- Mura : irrégularités dans un processus (exemple : variations dans la production d'un produit ou d'un service).
- Muri : difficultés soudaines pour accomplir une tâche (formation insuffisante, outils non adaptés...) créant une surcharge, un excès, des efforts inutiles sources de pression et de stress.
Mise en oeuvre : les outils du Kaizen
Encore une fois, le Kaizen n'est pas réellement une méthode, mais davantage un état d'esprit reposant sur des principes. Il existe toutefois un certain nombre d'outils pour s'inscrire dans cette approche.
Le PDCA
Le PDCA (Plan-Do-Check-Act) (ou roue de Deming) est un cycle d’amélioration structuré, utilisé dans de nombreuses démarches qualité. Il permet de faire progresser les processus d’entreprise en suivant une logique simple et répétable. Il s'emploi aussi bien pour optimiser les processus opérationnels que les processus de management. L’approche peut s’appuyer sur des outils comme le BPM (Business Process Management) pour piloter efficacement le processus d’entreprise.Ce mode de pensée s’inscrit pleinement dans une démarche d’amélioration continue du système et de ses méthodes de travail.Il est comprend 4 étapes :
Plan – Analyse et planification
C’est la première étape du cycle d’amélioration. Elle consiste à définir les axes d’amélioration. Elle se nourit de données en entrée provenant de différentes sources : dispositifs d’écoute, notamment l’écoute du client, constats issus d’un audit interne, dysfonctionnement relevé... Pour cibler les améliorations opérationnelles prioritaires, le pilote de processus et l'équipe de travail est en charge de définir précisément le problème, formaliser les objectifs et établir un plan d’action.
Do – Mise en œuvre
Phase opérationnelle, elle concerne le lancement / mise en oeuvre du plan précédemment établi. Les actions planifiées sont conduites par les personnes impliquées et avec les moyens définis. L’avancement des tâches fait l'objet d'un suivi rigoureux.
Check – Vérification et contrôle
Une fois les actions menées, on évalue les résultats au regard des objectifs. Comment ? En analysant les indicateurs, les retours du terrain, etc. Cette phase est essentielle pour identifier les écarts, détecter les réussites ou les points à améliorer. Cette phase permet de valider ou non l’efficacité des améliorations opérationnelles mises en œuvre.
Act – Ajustements et standardisation
Selon le verdict de la phase "Check", des ajustements éventuels peuvent être envisagé pour plus de performance notamment en cas d’écart manifeste. A l'inverse, si le succès est au rendez-vous, il peut être pertinent de généraliser ce qui fonctionne et d'intégrer ces nouvelles pratiques dans les standards. Cette étape permet de consolider les apprentissages et de faire vivre durablement la démarche d’amélioration continue. Le cycle d’amélioration peut alors redémarrer, enrichi des enseignements précédents.
Voir notre dossier pratique sur les étapes du cycle PDCA
Les 5 S
Centrés sur l'agencement de l’espace de travail, la méthode des 5S a pour objectif de rendre l'environnement proche organisé, secure et propre.
Cet acronyme reprend les lettres japonaises de :
- Seiri / Débarasser - Retirer ce qui est inutile
- Seiton / Ranger - Mettre en ordre
- Seiso / Nettoyer - Rendre l'espace de travail propre
- Seiketsu / Maintenir l'ordre - Adopter de bonnes pratiques pour conserver l'espace de travail rangé
- Shitsuke / Etre rigoureux : Pour mettre en oeuvre les 4S précédents
Pour en savoir plus, voir notre publication pratique pour comprendre les 5S
Autres outils :
- Le kanban : méthode "juste-à-temps" pour réduire les encours de production (Voir : qu'est-ce que la méthode Kanban ? ).
- Le management visuel : pour gagner en efficacité en utilisant des dispositifs visuels (affichages de KPI sur les murs, sur des afficheurs digitaux, etc.) pour transmettre des informations et objectifs.
Quels sont les bénéfices de l'amélioration continue ?
Outre les améliorations globales soulignées dans la définition, cette approche agit directement sur :
- la satisfaction des collaborateurs : par la prise en compte de leurs actions dans l'amélioration de leurs conditions de travail et l'optimisation de leur efficacité. Par la conduite du changement lorsque pour les nouvelles façons de travailler.
- la satisfaction des clients et leur fidélisation : avec des produits et services de qualité. L'écoute client est un outil important pour identifier les leviers de satisfaction client.
- l’optimisation des processus et des tâches : plus rapides, plus efficaces. L'efficience, l'amélioration des processus est au cœur du Kaizen.
- la réduction des délais et la réduction des coûts : grâce à une organisation plus performante. En ligne de mire, l'excellence opérationnelle.
- l'amélioration du travail d'équipe et de la coordination entre les services : par l'habitude de travailler ensemble.
Ce qui rend la communication plus fluide et décloisonne l'entreprise.
Ce qui revient globalement à améliorer la compétitivité et la rentabilité de l'entreprise : des produits de qualité supérieure au meilleur coût. Mais aussi globalement la réduction des risques : grâce à une organisation plus efficace, à un meilleur travail d'équipe et une détection précoce des vulnérabilités.
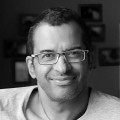
Auteur - Laurent GRANGER
Fondateur de Manager-go.com, Laurent partage depuis 2008 des outils et méthodes concrètes pour aider les cadres à mieux piloter leur activité. Diplômé d'une école de commerce et titulaire d’un DESS en diagnostic d’entreprise (IAE Lyon 3), il met à profit plus de 30 ans d’expérience plurifonctionnelle en entreprise, du développement commercial et marketing au pilotage organisationnel.
Auteur de plus de 800 contenus pratiques, lus chaque année par des centaines de milliers de professionnels, il s’attache à transmettre des approches applicables, alliant expérience terrain, pédagogie et sens pratique.
Un commentaire peut-être ?
Commentaires
chama borgi 7 mars 2021, 13:27 (Il y a 4 année)
Très intéressant, on va essayer de pratiquer cette méthode.
Il n'y a pas encore de commentaire.